They are being employed or working as labour is not so easy. The person has to go through several tasks in day-to-day life. If an individual is working in an industry where they produce products from raw material, they must be efficient in material handling.
Proper management of material will result in progressive outcomes and result in more production and more incentives. Before that person has to learn some primary material handling principles, although there are many principles, we will only have three core principles. Here we go:
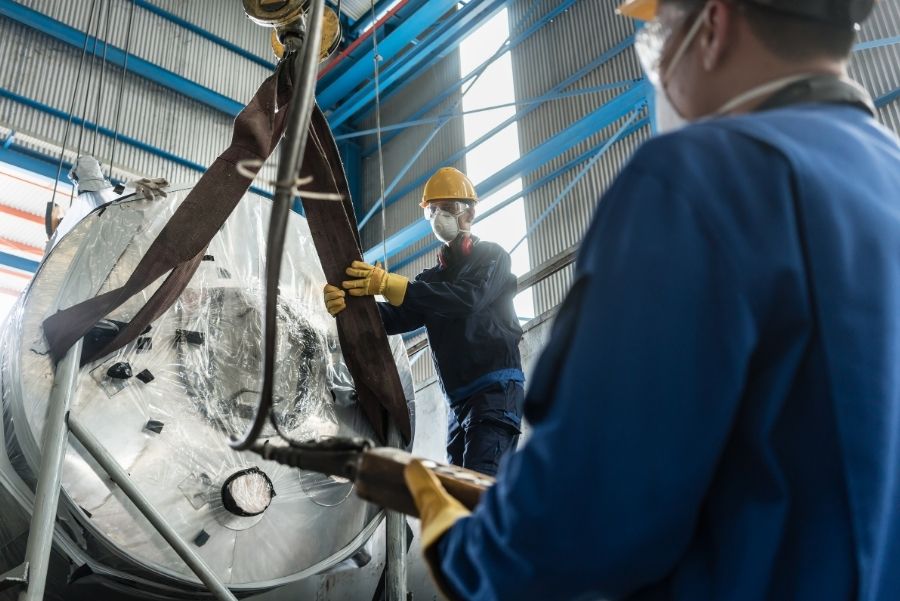
Forethought & Standard Maintenance
It comprises strategies before the execution of work. Critical thinking plays a crucial role here. It is just like a step-by-step guide for the success of a project. Employees need to consider various aspects of the project before working and create a to-do list or a concise plan. It will impart a significant effect on overall performance. Here aims, operationalization, and feasibility will be kept in view.
Standard maintenance states that techniques or procedures used in maintaining material must be compliant with standards set by quality assurance institutes.
Sometimes, flexibility and modification are required in the framework of employees’ operational structure; it will ensure better material handling. For example, the International Organization for Standardization set some standards for different kinds of industries.
So, every procedure or standard must be compliant with the standard set by ISO. It will be a sign of better performance with excellent product quality.
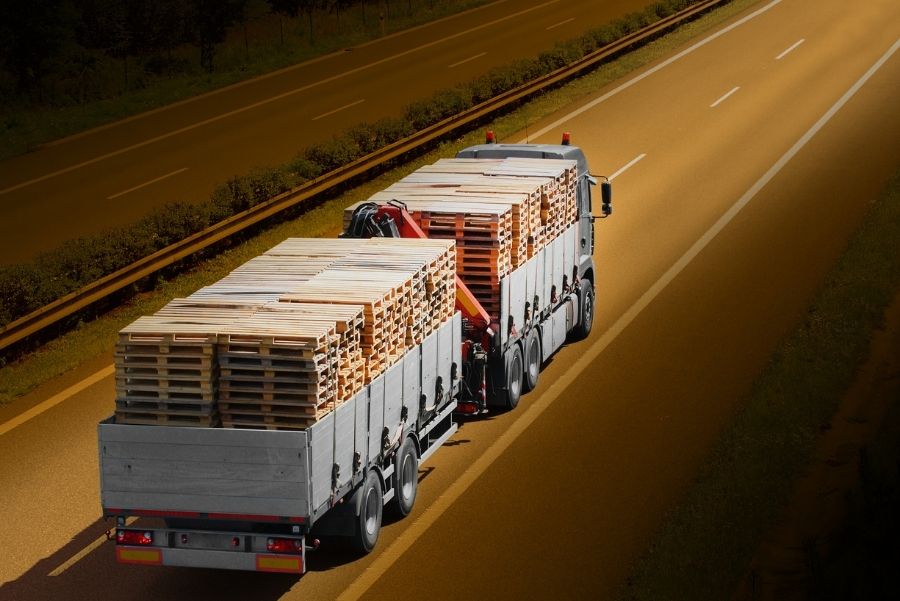
Human Capacity Bearing
Term somehow sounds wandering, but it is a scientific factor that talks about human capacity and work limitation. It is known as ergonomic. It states that work should not exceed human capability. It must be according to human rule.
No person should exceed his/her working potential. If he/she does so, they will encounter various health disorders. If a candidate works like a machine, eventually he/she will experience physiological and psychological conditions with no set limit.
Health will start depleting, ultimately affecting performance and the environment in the working space.
Excessive work ➜ No limitation ➜ Poor Health ➜ Less Outcome ➜ Disturbing working environment ➜ termination of employ ➜ an overall negative impact on industry and family.
Don’t consider employees as a robot. Humans need timely rest, as the body is following the biological cycles and rhymes. The body always syncs with time reference and still has limits. If someone tries to deny that limits and laws, he/she will suffer contingent ailment, which affects the organization’s reputation.
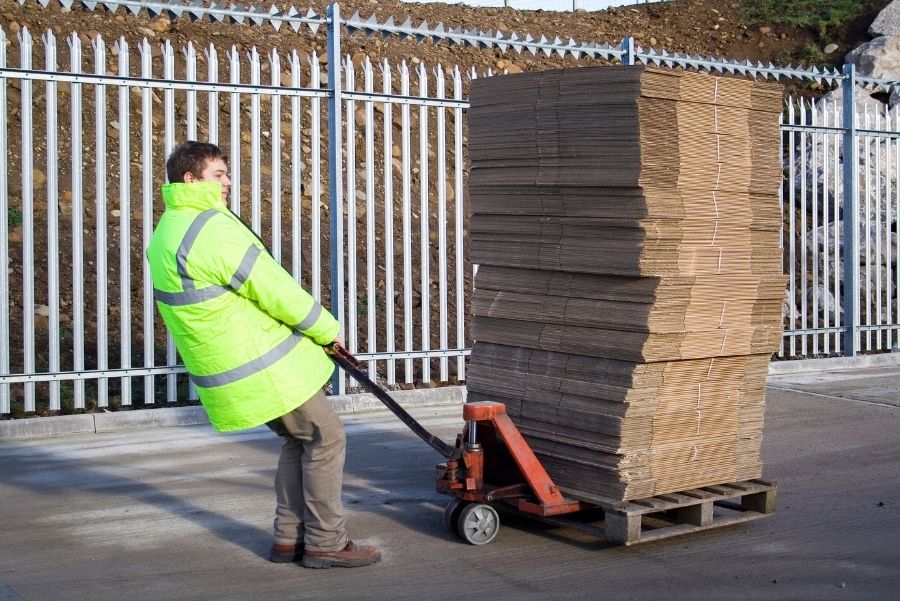
Environment-Friendly Automation
At present technology is advancing and astonishing the world with gadgets that perform the task efficiently better than humans. Automation refers to the utilization of electronic equipment for the completion of any job. It results in a smooth workflow, consistency, effectiveness, and increased yield of products.
Automation replaces the employees as work is being done by artificial humans like robots and other human assisting devices. The material will flow in a sequence with a series of events occurring spontaneously.
A sustainable environment is necessary for survival. Although technology is lifting every sector, it should be environment friendly. In the case of material handling, every aspect of the environment must be kept in view. Material handling or movement should not impact negatively. Whatever humans do with nature, nature will return in various forms.
So, try to handle material, keeping in view the principle of environment. We can take an example of a Nuclear plant implanted in Russia in1960 for the production of electricity but unfortunately, the rays emitted by that plant affect the lives of humans.
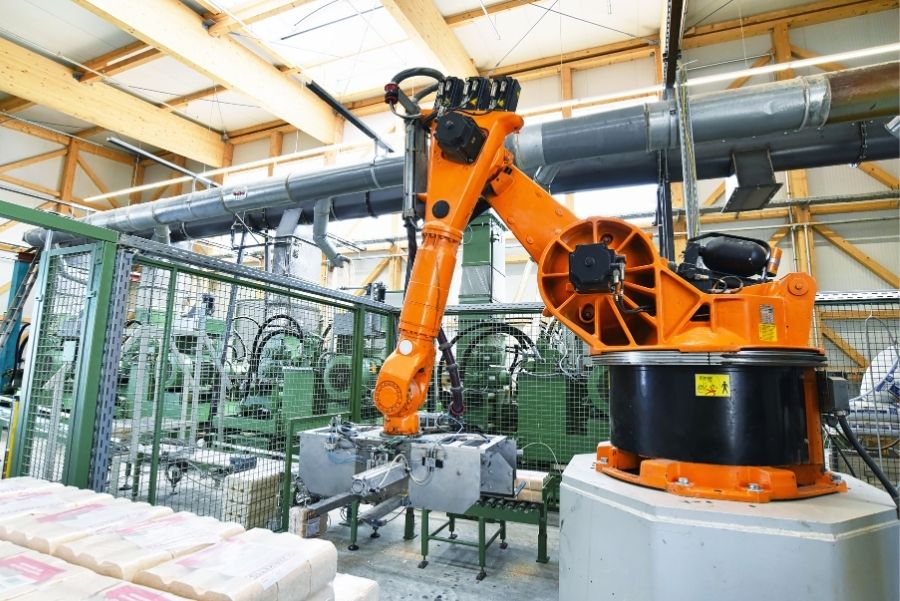